Scientists Produce Solar Panels From Solar Energy And Say It Will Reduce Costs
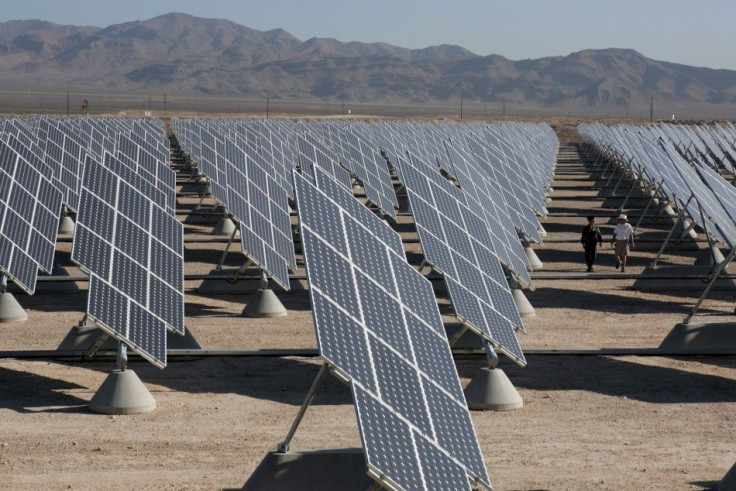
Chemical engineers at Oregon State University are capturing the sun’s power to produce not only solar energy, but also the materials to create the solar panels and the technology that could cut solar energy costs and production time.
“Our system can synthesize solar energy materials in minutes compared to other processes that might take 30 minutes to two hours,” Chih-Hung Chang, lead author of the study and a professor of chemical engineering at the university, told the Daily Fusion. “This gain in operation speed can lower cost.”
The researchers’ findings were published in late March in RSC Advances, a journal of the Royal Society of Chemistry and supported by the National Science Foundation.
The team uses a “continuous flow” microreactor to produce nanoparticle inks that make solar cells by printing. Artificial sunlight, to allow precise temperature control and aid the quality of the finished product, is focused on the solar microreactor to zap it with heat. The same process can be used with direct sunlight, at a fraction of the cost of current methods.
“Several aspects of this system should continue to reduce the cost of solar energy, and when widely used, our carbon footprint,” Chang said. “It could produce solar energy materials anywhere there’s an adequate solar resource, and in this chemical manufacturing process, there would be zero energy impact.”
Copper indium diselenide was used to make the solar energy materials, but to lower material costs, copper zinc tin sulfide could be used, Chang said. The process could even continue 24 hours a day, if sunlight is used to make molten salts that could power the manufacturing process at night.
In the lab, thin, chalcogenide-based film solar cells have converted solar energy at 20 percent efficiency while costing less than silicon technology. Efficiency should improve, the researchers say, and the thin film (1-2 microns versus the 50-100 microns of conventional silicon cells) would be easier to incorporate into windows, roof shingles and other structures.
© Copyright IBTimes 2024. All rights reserved.