Automotive Recalls Will Only Increase, But It’s Not Why You’d Think
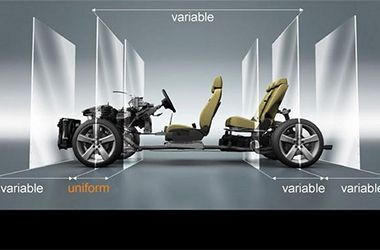
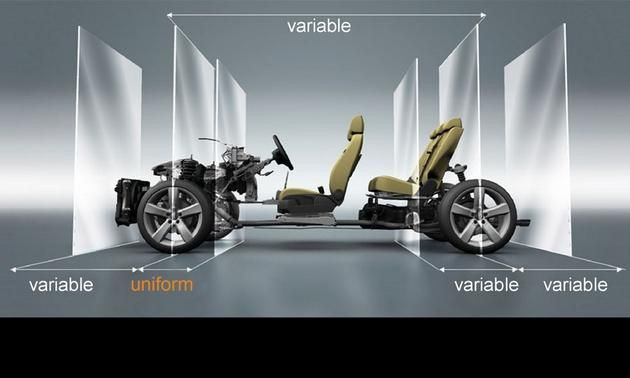
“Recall” is a dirty word in the automobile world.
The 9 million vehicles General Motors and Toyota have recalled in recent weeks have incited public panic. The large scale reflects a characteristic of modern automotive manufacturing: Today’s vehicles share a staggering number of “modules,” various pieces of equipment engineered to fit cars across models and classes. For example, Toyota implements the same airbag system in the Camry, Corolla, Yaris and Highlander among other models in the U.S. and around the world.
Most manufacturers share a variety of parts among models; General Motors’ Detroit plant currently builds the Chevrolet Volt, Malibu, Impala and Cadillac ELR, despite the massive variation in styling and class designations (compact, mid-size, and full-size). Underneath the different bodies and interior styling, the cars are comprised of the same modules.
Nearly all of the everyday, normal vehicles purchased are connected by platforms and components. This practice isn’t limited to one class or line of vehicles, however. Karl Brauer, senior editor of insights at Kelley Blue Book, said these massive recall numbers are the nature of the beast.
“That’s how you get those crazy [recall] numbers -- shared platforms,” he said.
But parts sharing in itself is by no means a new economic tactic. Brauer explained that the idea of the interchangeable part is as old as Henry Ford’s Model T, but that was the only model using identical parts. More recently, General Motors’ 1964-1981 "A Body" platform was the base of the Pontiac GTO, Chevrolet Chevelle SS, Oldsmobile 442, Buick Regal GS, and others. Those cars, Brauer said, would have different engines and suspension, “but they were really the same car.”
What the new "modular" style helps manufacturers do is utilize the same basic platform for multiple vehicles spanning multiple classes (mid-size and full-size cars to their equivalent "crossover" variants). That in turn means that far more cars use much of the same components; hence the 6.4 million number Toyota released.
Brauer said that carmakers only started sharing entire systems across multiple classes in the modern era (late '80s to early 2000s). “A Honda Odyssey -- that looks like a separate car, but it’s just a stretched Accord. A [Toyota] Rav4 is a taller Corolla. They’re nearly the same thing.”
Vehicles will only become more universal; Volkswagen Auto Group, which produced 9.7 million vehicles last year, has begun to implement MQB - Modular Querbaukasten (English: modular transversal toolkit). What this manufacturing system does is designate a series of unchangeable points on a chassis (the underpart of a vehicle; a metal frame). Everything aside from these points is interchangeable. VAG designs multiple cars along these common points; any vehicle with a similar engine layout will be on a shared platform.
Instead of building individual chassis to put a few separate models on, Volkswagen will build one base and add differing mechanical pieces like axles. Eventually, VAG expects to produce 40 of its vehicles on this architecture -- everything from the supermini Volkswagen Up! to large crossover SUVs like the Audi Q7.
That will increase profit margins -- computer and electrical-based systems are rather expensive, as is developing new chassis. Fewer unique parts means less money spent to design and stock differing pieces. This is the future of automotive manufacturing.
“The more parts [manufacturers] can share,’” he said, “‘the more money they can save.”
That’s why they’ll be sharing more recalls, too.
© Copyright IBTimes 2024. All rights reserved.