GE Lends Helping Hands To Jet Engine Suppliers To Sidestep Supply-chain Challenges
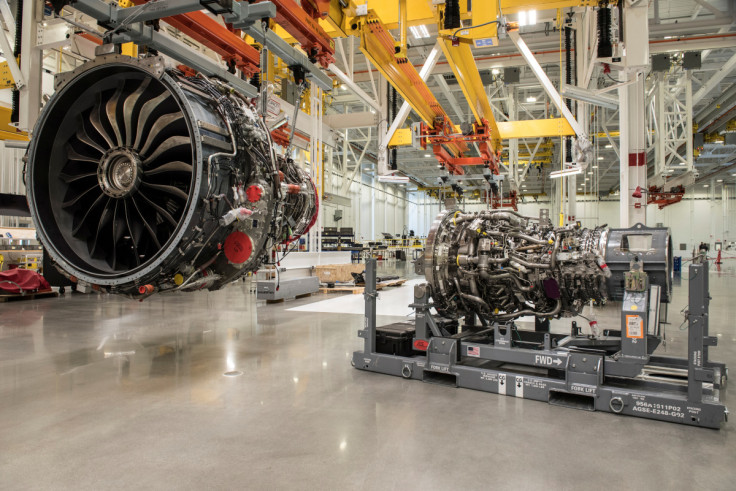
General Electric Co sent 12 machinists from its Rutland, Vermont, facility across the country last fall to help a sub-supplier in Arizona that was so short of workers it could not add a second work shift.
GE's action on the day after Thanksgiving was not an isolated case, Chief Executive Larry Culp said. The company has deployed its machinists and hundreds of engineers to suppliers and sub-suppliers in the United States to address the bottlenecks that are hampering production of its jet engines.
The measures are working. For example, its engineers last year also helped a supplier reduce inspection time for a critical rotating part used in a jet engine to 30 minutes from 6 hours, company executives said.
Yet Culp said it is a "daily battle" to keep up with booming demand at the company's aerospace unit due to persistent shortages of labor, parts and raw material.
The unit, which supplies and services engines for Airbus and Boeing Co aircraft, had unfilled customer orders worth $135 billion at the end of 2022, up 8% from a year ago.
The problem is more acute with the supply base for LEAP engines, which GE produces in a joint venture with France's Safran.
The backlog for LEAP engines, which power the narrowbody aircraft of Airbus and Boeing, has increased to 10,000 units. Adding to complexity, just 10% of the 2,500 parts used in engines for Airbus' 320neo and Boeing's 737 MAX planes are common.
"There's no one commodity. There's no one component which is the issue," Culp told reporters on the sidelines of GE's annual investor meeting on Thursday. "There's no one prime problem, but it's widespread."
GE is not alone. Other engine makers are grappling with similar challenges, making it tougher for aircraft makers to increase production.
A shortage of aircraft has constrained airlines' plans to ramp up capacity and capitalize on booming travel demand. Delays in jet deliveries are pushing some of them to extend their leases, driving up lease rates.
Culp attributed the supply-chain challenges to the pandemic, which led to a plunge in air travel demand, forcing the aviation industry to lay off thousands of workers. At the height of the pandemic, GE itself announced plans to cut the workforce at its aviation unit by up to 25%.
The industry's head count has gone up since then. But Culp said having too few workers with "institutional knowledge" remains a problem.
GE's senior leadership team now conducts a weekly review of the supply situation - component by component, supplier by supplier. It is carrying excess inventory of parts in short supply, increasing its costs.
The company is also helping suppliers cut waste and improve turnaround time to boost productivity. In one instance, GE helped one supplier start producing five low-pressure turbine cases for engines per week, up from that same amount per month.
Similar measures at GE's facility in Terre Haute, Indiana, have helped boost production of jet engine turbine frames by 70%.
GE managed to increase the output for LEAP engines by 34% in 2022 from a year ago. It is aiming to increase the production by about 50% this year.
© Copyright Thomson Reuters 2024. All rights reserved.