As inland China grows, contest intensifies for labour
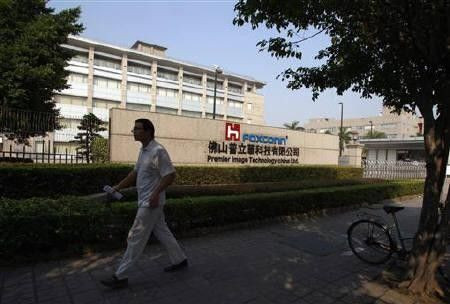
He Shuaixing shakes his head listening to the pitch from a job recruiter on a cold wet day in a factory district outside Shenzhen , epicentre of China's export machine.
The 26-year-old from the poor heartland province of Henan, like so many other workers, had just returned from his village after the Lunar New Year holidays and was looking for a job. But unlike an older generation of migrant workers, not just any job.
It's easy to find work, but not easy to find good work, said He, wearing a thin grey jacket and a flop of gelled hair. We haven't seen any big improvements in wages or benefits.
Besides, the booming metropolis of Shenzhen was getting too expensive, he complained.
Labour shortages in Chinese coastal factories are nothing new. The world's workshop has been churning out the exports again after hitting a lull during the global financial crisis. But workers like He are becoming more choosy about the kind of jobs they want, eschewing the long hours, tedious work and poor benefits offered in China's many sweatshops.
What's more, competition for labour is now coming from new factories in China's rapidly urbanising interior.
Chongqing (formerly Chungking), in southwestern Sichuan province and one of China's biggest cities, has launched a Spring Breeze Action campaign to recruit workers from the coast.
It has raised monthly blue-collar wages to around 1,200 yuan ($183), and is offering 300-yuan monthly subsidies to workers who take jobs in local factories.
Around 40,000 signed up on the first day alone. The wage in Chongqing compares to 2,000 yuan in southern China's manufacturing belt.
In Henan, a giant new Foxconn factory making iPhones will need several hundred thousand workers.
Fuyang, in eastern Anhui province -- a quarter of whose 9.5 million residents were migrant workers -- has recently dangled perks such as housing subsidies, TV-equipped dormitory rooms and health insurance to entice labour to its new factories.
In response, authorities in some coastal regions have hiked minimum wages, raising expectations for further pay rises this year among workers squeezed by rising inflation.
Guangdong province, home to the Pearl River Delta, one of China's main manufacturing hubs, will raise minimum wages by an average of around 19 percent next month. Many factories, in fact, are already paying well above the minimum wage to retain and lure skilled workers.
MORE RECRUITERS THAN JOB-SEEKERS
Yiwu, a small city in coastal Zhejiang province is famous for the cheap goods it makes at hundreds of factories and workshops -- arts and crafts, hardware, cosmetics, household goods -- and exports around the world.
Job fairs had sprung up around the teeming market stalls after the New Year holidays and recruiters were shouting and waving cardboard signs. They seemed to outnumber the few job-seekers wandering about.
Other recruiters were sent to train stations to be the first to welcome migrant workers returning from the interior -- and escort them to a factory gate.
Last year we were bringing carloads of workers back to our factory. It was very quick, said Wang Xia, a recruiter for a cosmetics factory sitting at her booth in an outdoor market.
New workers this year are asking for much higher starting salaries than older workers at her factory, she said.
This is impossible, she fumed. For this year, we have already increased our salary base and working benefits. This year, there are many job seekers who are just basically browsing around. The situation is most severe.
The labour tug-of-war may well intensify.
Standard Chartered Bank thinks China, with its one-child policy and transforming economy, will only generate three million new labour market entrants a year during 2011-15, compared with some 10 million a year in recent decades.
The slowing growth (and then decline) of China's labour pool will clearly be negative for China's potential growth rate, wrote Standard Chartered economist Stephen Green in a research note titled 'Wanted': 25 million workers.
WORKSHOPS CLOSING
Despite the need for workers, many smaller factories operating on low margins and squeezed by recent sharp spikes in raw material prices, were unwilling to improve benefits, having already been forced to raise prices of their goods.
Some experts say the strains could accelerate industrial upgrading, automation and consolidation. More labour-intensive factories will close or move inland where cheaper land and labour often compensate for less developed supply chains and higher transport costs.
Other factories have quit China altogether, moving to lower cost countries such as Vietnam and Bangladesh.
I believe that some of the pressures now are even more serious than during the (2008) financial crisis, Zhou Dewen, the head of Wenzhou's Small and Medium Business Development Association, told Reuters Insider Television.
If the (government) doesn't take good measures, this may cause 20 percent of factories to stop production, halt production or even shut down completely, Zhou added.
China's rusting, labour intensive coastal factories may be fighting a losing battle.
After the global financial crisis, which severely hit China's export-reliant $6 trillion economy, a shift seems apparent in government thinking.
The policy is clearly tilted toward boosting household income and creating a more consumption-led economy, to be less dependent on low-margin manufacturing exports, and travel up the value chain in manufacturing advanced technology products.
A relatively cheap yuan was once paramount in preserving the competitiveness of China's cheap exports. But the increasing importance of the consumer to the new economic equation argues for a stronger currency and higher wages to narrow the wide wealth gap between rural and urban areas.
For now, China's healthy export growth -- 37.7 percent in January from a year earlier -- has sustained a still substantial export engine, which some economists say accounts for around a fifth of its total economy.
But China's growing thirst for commodities -- imports overall in January surged 51 percent -- have contributed to a sharp spike in raw materials, whose rising costs pose an even more potent threat than higher wages for some factory owners.
RISING INFLATION
Anil Mirwani, co-founder of NV brand jeans which retail in the United States and are made in a factory in Guangdong province, says wages only make up around a quarter of his total costs whereas fabrics make up around 55-60 percent.
It's insane, he said of sharp rises in cotton yarn prices in China amid chronic global shortages of cotton supplies.
We can cope, but it's been a real problem for us.
Clothing chains such as Esprit and Hennes & Mauritz warn that raw material cost inflation could trickle through to prices and hurt budget clothing sales.
Global consumer goods exporter Li & Fung Ltd expects prices of products sourced in China to rise at least 10 percent in the first half of the year as costs escalate.
For China's vast army of 153 million migrant workers,
the sting of rising inflation is growing, including food and rentals for the basic, often tiny rooms that are popular accommodation for millions in factory towns.
Despite bitter complaints about soaring prices, workers say they can scrimp enough to save at least a chunk of their wages.
While last year a spate of strikes crippled production at multinationals in China such as Honda Motor Co, few expect that kind of labour unrest this year with wages rising, if not as fast as many would like.
There may be a small percentage of people that go on strike because the wages are too low, said Huang Hong, a veteran job recruiter in one of around 40 booths at the Wenzhou employment vocation centre that was teeming with migrant workers.
But people will tend to quit rather than go on strike.
© Copyright Thomson Reuters 2024. All rights reserved.