Making Your Production Sustainable
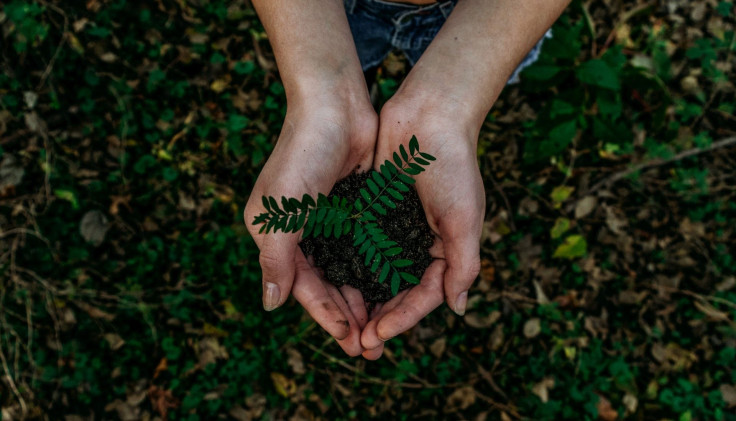
The federal government reports that industrial operations use about one-third of the overall amount of energy produced in the U.S. annually. To create a sustainable future, manufacturing companies will need to play an important role.
The good news is that manufacturing engineers are already waking up to the challenge, mainly design and manufacturing engineers. Products that use less energy, minimize waste, and remove emissions are built by engineers every day and manufactured in sustainable ways.
Yet more work needs to be done. And engineers are challenged by current economic and environmental issues to optimize production processes.
There are six main steps you can take to make your production more sustainable. The first two are standard, and many companies do a decent job. But the four following elements are areas that design engineers constantly need to worry about.
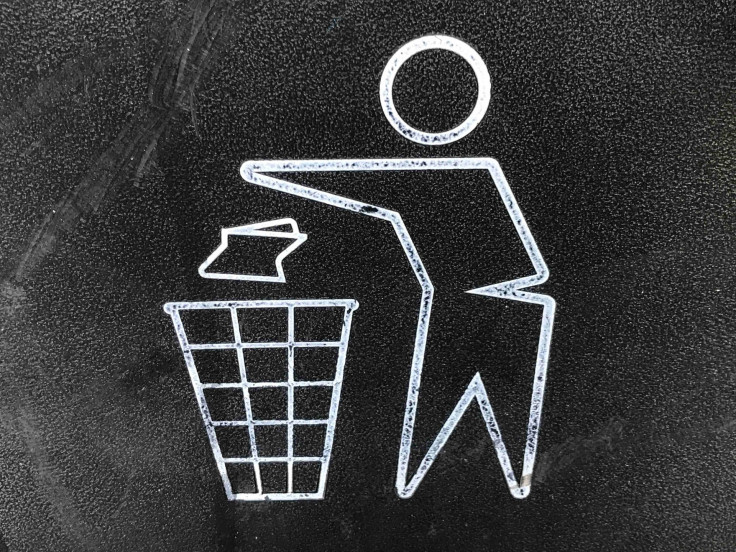
Optimize the Current Use of Fossil Fuels
Cutting energy prices is a win-win scenario in today's world. There seems to be little doubt that we're close to "peak oil," i.e., the point when we've depleted half of the world's estimated oil reserves. The only argument left is when the supply shortage will begin or if it has already begun.
Save fuel today by turning off the machines when you're not using them. Replace a single-speed motor with a variable-speed or servo drive to decrease energy consumption. Use a variable-speed hydraulic pump in production where possible. Also, take a look at other sources of renewable means of energy, including wind, solar, or hydropower.
Reduce Waste
To produce the finished product you need, consume only the materials and power. It sounds straightforward for us today, but I think we all know that our primary goal in the past has been to reduce production costs or time to market.
Nobody knew or cared if we used more than we wanted. If it's the amount of metal, paper, or packaging material used, this applies to every industry. Examine again whether it's possible to justify the option of investing in precision manufacturing equipment by looking for ways to reduce waste to a minimum.
Cut Down on Emissions
When I meet colleagues at conferences or trade shows, one of the hot topics is how to reduce the use of "environmentally unfriendly" materials in manufacturing and by-products of production processes. I hear people keen interest in dry, or near-dry, machining. When removing metal, using as a little coolant as possible.
De-burring, or taking the burrs from finished material after you've cut it, is another method that uses quite a few powerful chemicals.
Recycle Responsibly
Look at the number of metal chips created in the processes of machining and finishing. People used to fill enormous hoppers and move them to a recycling plant. Now they're beginning to look at the energy costs involved with all of this.
"Chip making," machines compress chips, remove the coolant, and shape the metal into small spheres, which are much easier to transport and consume much less energy, are one solution. Or, better still, they could invest in in-house chip handling equipment, one that processes them into tiny billets that can be recycled on-site.
Recover Energy
Hybrid cars retrieve energy otherwise lost during braking. Did you know machines can do the same thing? Power-sharing has its origins in machine tools, where a single power supply shares power with the servos used in metal cutting machines and seaming machines. In fact, during deceleration, we can take control and return it to the main lines. The energy was lost in the past, turned into heat, like the brakes on a vehicle.
Another excellent example is how certain operations can organize the cycles of many metal presses. At first, you would think, "Make all the presses go up and down together and then move the material." That doesn't affect process time, it doesn't affect cycle time, and it doesn't cost more--but it saves resources.
We have begun to extend our shared servo control experience to other industries such as packaging equipment, automation, and printing presses.
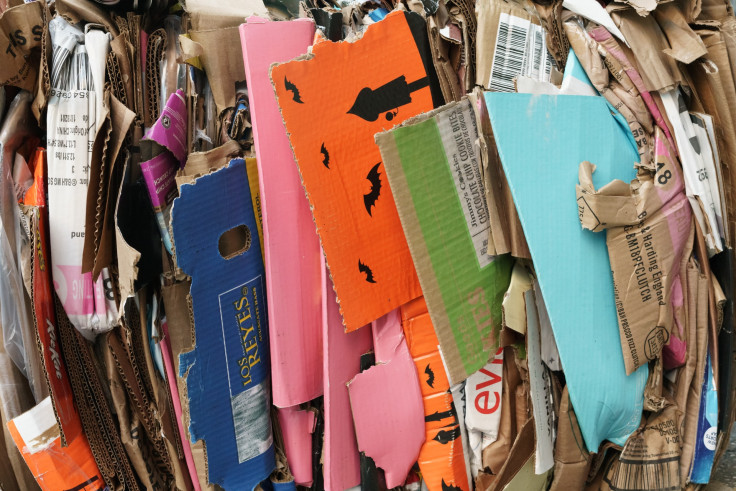
Save Time
Just saving time is, by itself, an indirect saving of energy. If you can run a loop faster without using more resources, you can shut it down and save electricity. Or, if it's a large-scale manufacturing plant, you can reduce the number of machines you need to manufacture the same quantity of material.
These are all problems that engineers face, and they're what will make development sustainable in the coming years. Do you have people in your company who just love a good challenge? They naturally think, "How can I make this product use less energy?"
Unfortunately, most people's minds turn to "big-ticket" options like solar and wind farms when they hear about sustainability. But while the resources to get all the publicity might not be available, the "workhorse" machines, like servo drives, hydraulic pumps, and bearing assemblies will provide a sustainable output for the future.
© Copyright IBTimes 2024. All rights reserved.