NASA Testing Shape Memory Alloy For Foldable Aircraft Wings During Flight
In a series of recent trials, NASA successfully tested a new lightweight material to fold the outer portions of aircraft wings during flight. The material can be applied to both subsonic and supersonic flights, and will improve the aerodynamic ability of both, the space agency said Friday.
The new material is a shape memory alloy, and is triggered by controlling the temperature, moving the outer wings up or down to desired angles. While present-day aircraft have the ability to fold their wings, they rely on motor and hydraulic systems which are both bulky and heavy, making planes relatively cumbersome.
In contrast, systems using the new alloy could weigh 80 percent less than traditional motor and hydraulic mechanisms. Its testing is part of NASA’s Spanwise Adaptive Wing (SAW) project, on which Boeing Research & Technology and Area-I are partners, and it was carried out at the agency’s Armstrong Flight Research Center in California.
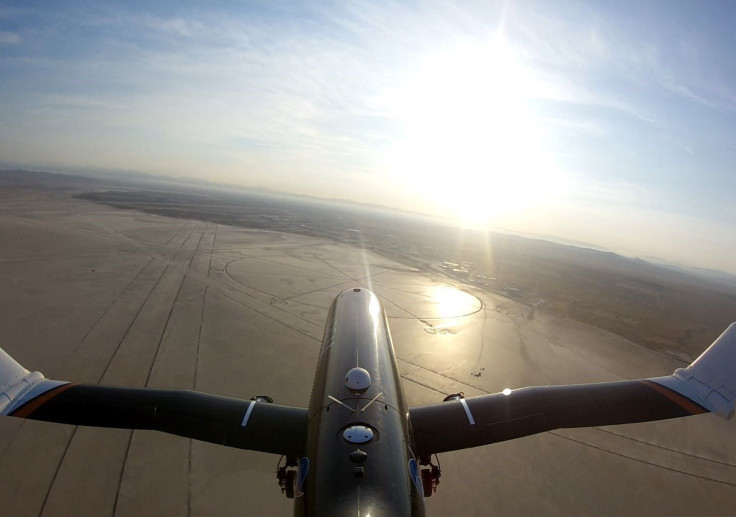
The tests showed the new alloy allowed the wings to be moved during flight, moving to various angles to maximize the aerodynamic benefit of the wings’ shapes. In its statement, NASA said the potential benefits in commercial subsonic flights include reduction of aircrafts’ weight, making them more fuel-efficient, and giving pilots the opportunity to take advantage of various flight conditions, by folding the wings to adapt. But the real benefits are in supersonic flight.
"There’s a lot of benefit in folding the wing tips downward to sort of 'ride the wave' in supersonic flight, including reduced drag. This may result in more efficient supersonic flight. Through this effort, we may be able to enable this element to the next generation of supersonic flight, to not only reduce drag but also increase performance, as you transition from subsonic to supersonic speeds. This is made possible using shape memory alloy," SAW Principal Investigator Matt Moholt explained.

The heat-triggered shape memory alloy was developed at NASA’s Glenn Research Center in Cleveland, Ohio, and it was built into an actuator by Boeing, while the aircraft used for testing — Prototype Technology-Evaluation Research Aircraft, or PTERA, a drone shaped like an airplane — was designed and built by Area-I.
"The performance of this new alloy that we developed between NASA and Boeing really showed outstanding performance. From the time we started initial testing here at Boeing, up to the flight tests, the material behaved consistently stable, and showed a superior performance to previous materials," Jim Mabe from Boeing said in the statement.
The SAW test flights were conducted over two days, and included a number of maneuvers, heating and cooling the actuators to change the angle of the PTERA wing panels between zero and 70 degrees, upward and downward.
"PTERA was developed as a flying laboratory, and was used in this flight series to host the SAW experiment. The intentional, in-flight actuation of the outboard wing panels was a historic event, made all the more special as it took place over Rogers Dry Lake, where so much aviation history has been written," Area-I CEO Nicholas Alley said.
More SAW testing is planned for summer 2018, which will also attempt both upward and downward wing folding in the same flight. NASA is also working on scaling up the technology for testing in an F-18 jet.
© Copyright IBTimes 2024. All rights reserved.