Nissan To Improve Car Production Using Advanced Robots and New Manufacturing Technique
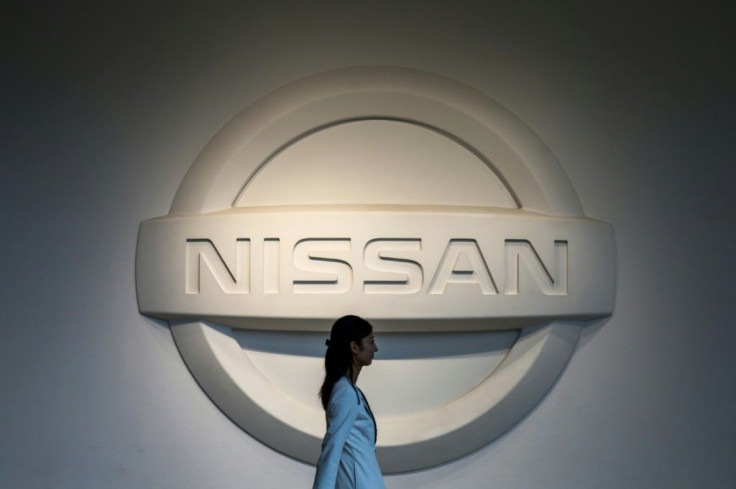
Robots have made their mark in today’s business world, especially in the manufacturing industry, where they are deployed in large numbers. Robot development is growing fast, and there is no indication that this development will slow down in the next few years. In some manufacturing plants, like in the auto industry, robots play a crucial role and even revolutionize how cars are being made.
At Nissan’s Production Engineering Research and Development Center, researchers have come up with a revolutionary way of manufacturing low-volume components like replacement parts for vehicles. Nissan called it the dual-sided dieless forming. This new manufacturing technique can revolutionize the way car components are made. It can make low-volume components out of metal sheets without the need for those massive tools, like forming dies. Nissan’s new manufacturing technique can tremendously lower upfront costs and make the production of low-components an economically attractive proposition, according to The CNET.
In manufacturing, a fender requires a traditional tool like forming dies. These tools are used to force metal sheets into the desired shape. However, these tools are massive and quite expensive to maintain. This is where exactly Nissan’s breakthrough comes into play, to replace those traditional tools with robots. The new method involves a pair of synchronized robots, working together to complete a certain task. Robots are placed on each side of a fresh metal sheet, which held firmly in a frame. Precisely controlled by the computers, the robots start working on the metal sheet, molding it, creating a shape as required.
In addition, Nissan also detailed how they addressed some technical concerns. First, the company used more advanced computer controls that will allow the robots to work with greater precision and deal with more complicated tasks. The company also added a mirrored-diamond coating to the forming tools, which, according to Nissan, reduces friction and eliminates the need for lubrication. The use of mirrored diamond coating resulted in much finer finish quality. It also improves consistency and, more importantly, its lower manufacturing costs. Then, finally, Nissan developed logic programs for robots to improve the quality of work further.
Nissan’s latest breakthrough, the dual-sided dieless forming process, promises a more cost-effective way of producing low-volume components for older car models. Right now, it still unclear if Nissan has plans to commercialize or share this latest manufacturing technique with other manufacturers.
© Copyright IBTimes 2024. All rights reserved.