Smart Supply Chains: Rethinking The Food Recall Process
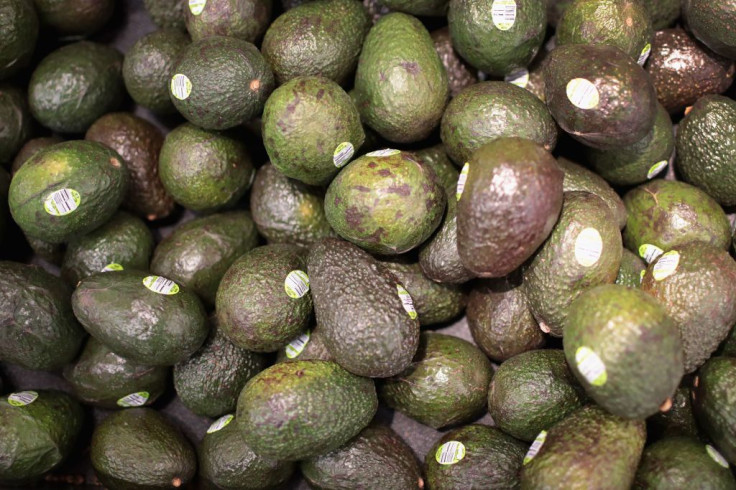
To the dismay of avocado lovers nationwide, Henry Avocado Corporation issued a recall in March for its avocados sold to retail stores in six states. The coveted fruit was recalled due to potential contamination with the bacterium listeria monocytogenes.
This recall likely hit the avocado giant hard, since the average food recall in the United States is estimated by the Grocery Manufacturers Association to cost between $30 million and $99 million. And that figure only includes the direct costs companies incur from retrieval and disposal of recalled items — there are also the indirect costs resulting from lawsuits, reputational damages and sales losses.
Food recall instances will likely only increase due to declining food inspection standards in the U.S. But with the rise of IoT and blockchain technology, the consequences of a food recall don’t have to be so harsh, as the tech facilitates efficient tracing of food infection sources.
How can Henry Avocado — and all other food distributors hit with a foodborne illness outbreak — be more transparent with consumers while also reducing their own potential losses?
Uncertain times ahead for food recall
Between 2013 and 2017, the volume of food recalls increased dramatically, and Class 1 recalls of meat and poultry increased by 83 percent. According to the Centers for Disease Control and Prevention (CDC), one in six Americans will contract a foodborne illness annually, and as standards become more lax, that number is sure to go up. While technology can fill in the gaps that decreased inspection requirements introduce, it currently plays an underwhelming role in the food recall process.
When reports of a foodborne illness come in, state health departments contact the CDC, after which the CDC contacts the Food and Drug Administration (FDA) and the Food Safety and Inspection Service (FSIS). Recalls are typically issued on a voluntary basis by the food distributor it’s traced to, but if not, the FDA and FSIS can request a recall, forcing the distributor to legally comply.
The message is then put out to consumers via news reports. But a consumer who doesn’t get the message in time and has one or more infected product sitting in their kitchen could potentially put their own life in danger.
How the food industry can turn it around
According to the U.S. Public Interest Research Group (PIRG), food distributors should adhere to a four-point safety plan for food distribution — testing, inspection, traceability and recall.
The traceability step offers the biggest potential for improvement, given rising tech trends, including IoT and blockchain. The food distribution sector has the opportunity to overhaul the tracing of foodborne illness and the communication process of alerting the public — an especially attractive prospect, considering foodborne illnesses may be on the rise thanks to lax food inspection.
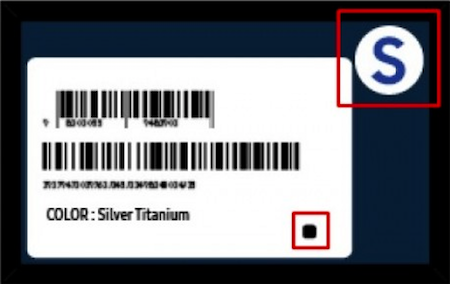
Smart labels will play an increasingly important role in evolving how government agencies, food distributors and consumers communicate during the recall process. By integrating IoT and blockchain to create smart barcodes, both consumers and facilitators of the food supply chain will be able to scan the barcode with a smartphone and understand where the food has come from.
Having access to a product’s entire history helps food companies and government food safety agencies pinpoint the source of a foodborne illness. Rather than pulling millions of units out of the supply chain, the intelligence gained from smart labels can instead allow for only thousands to be pulled, lessening the financial hit to food companies. And when a recall is issued, consumers can scan the label on the recalled product in their fridge to understand if they should toss it in the trash or if it’s safe to eat.
Smart labels can also help the misinformation process that may accompany a food recall. If one kind of vegetable is recalled, social media and the web allow misinformation to spread about what kind of bacteria is involved, where the recall exists and what foods are affected. Smart labels allow food distributors and food regulatory agencies to deliver a message straight to consumers and cut out misinformation.
Food corporations no longer have to settle for losing millions of dollars while scrambling through the recall process. IoT and blockchain have the potential to transform food recalls from mad scrambles into orderly, communicative processes. With the emerging tech entering the market, food distributors must look for the right partners to make this idea a reality for their own supply chains.
Scott Fletcher is CEO and Billy Meadow is the founder and chief technology officer at LocatorX, a company that develops tracking technology based on nanomaterials.
© Copyright IBTimes 2024. All rights reserved.