Stanford researchers work on low-cost medical ventilator for global disasters
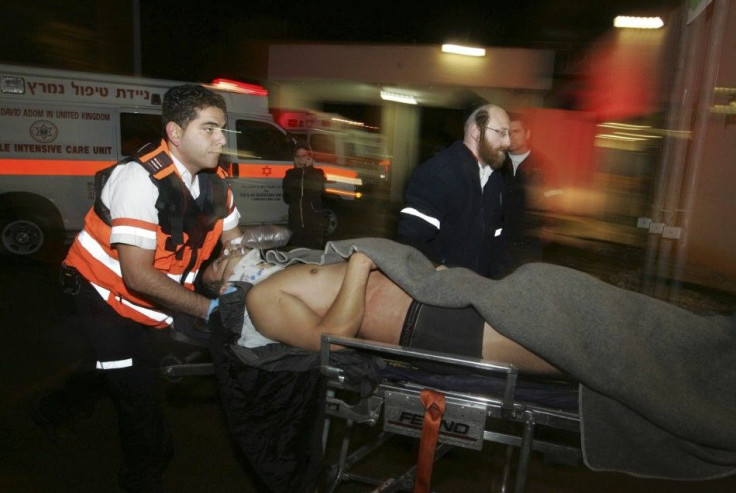
What began with a few sketches on a napkin over lunch with a physician friend has now evolved into a breakthrough innovation in bio-design, in the form of a low cost ventilator that is expected to bridge, in part at least, the overriding global shortage of these critical medical devices.
The low-end model, called OneBreath, was designed by a team of researchers led by Matthew Callaghan, MD, at Stanford Biodesign, a training incubator in medical technology that brings together multidisciplinary teams of medical, engineering, law and business school students to address unmet medical needs with innovative approaches.
Callaghan says that the idea struck him first at a planning meeting at a hospital that was trying to formalize criteria to decide which type of patients would receive life support from the limited number of ventilators in the hospital should a scenario arise when emergency demand outstrips supply. Later, an alarming piece of statistics - that the United States would fall short of 700,000 ventilators in the event of a moderate-to-severe influenza pandemic - triggered the thought of commercialization of the innovation.
In line with the credo of Biodesign, Callaghan and his team spent three months on clinical observation, asking questions, identifying needs, analyzing markets and brainstorming concepts. Along the way, they also learned about managing intellectual property, the regulatory process and medical reimbursements and applied these knowledge to their specific project. This also helped them arrive at a well defined need - both in terms of device design and a potential market in the developing countries where explosive population was ill-paired with a serious dearth of emergency infrastructure.
As reported by Spectrum, the Stanford Center for Clinical and Translational Education and Research, the OneBreath team lowered manufacturing costs by reducing the number of parts; airflow is measured and controlled with propriety software rather than hardware. To ensure operability and portability during natural disasters, the compact plastic housing is rugged, grime-resistant, stackable and easy to carry. To cope with power outages, units come with a seven-hour rechargeable battery.
Keeping in mind the possible lack of expert technicians during such disasters, the units have been so designed as to make it possible for novices to operate and repair them; a breathing tube replacement costs 50 cents, rather than the $180 required for the same process in high-end ventilators!
With a targeted cost of under $800, OneBreath's retail price should be a fraction of comparable ventilators. Thus it should realize Callaghan's initial vision of making it possible and affordable for governments and institutions to stockpile units for potential disasters.
The overall project has truly been a multidisciplinary effort; When we needed a business plan, we visited the Stanford Graduate School of Business, and three students wrote our plan as part of a class assignment. After we built our first cardboard prototypes, we went over to Stanford's pulmonary and critical care office with donuts and coffee, and the physicians were happy to provide user feedback, Callaghan is quoted by Spectrum.
The product has received wide acclaim so far, having been named a Popular Science Invention of the Year in 2010 and winning awards from the American Association for Respiratory Care, the American College of Surgery Clinical Congress and NCIAA BMEidea. However, Callaghan estimates that it will take at least another year and $2.5 million for the commercial launch of OneBreath, after completion of final testing, agency approvals, pilot manufacturing and lockdown of technical documentation.
© Copyright IBTimes 2024. All rights reserved.