Supply Chain Risks Every Manager Should Look Out For In 2023: Vikas Gupta, Supply Chain And Logistics Expert
The last two years have been turbulent for global supply chains as companies were forced to navigate through supply upsets brought on by the global COVID-19 pandemic, mass labor shortages, and the recent geopolitical crisis in eastern Europe. In 2021 45 percent of economists had expected the supply chain bottlenecks and other hurdles to recede by 2022. However, with only a month left for 2022 to end, and seeing how these problems have still not been resolved supply chain 2023 looks like it is going to be an equally challenging year.
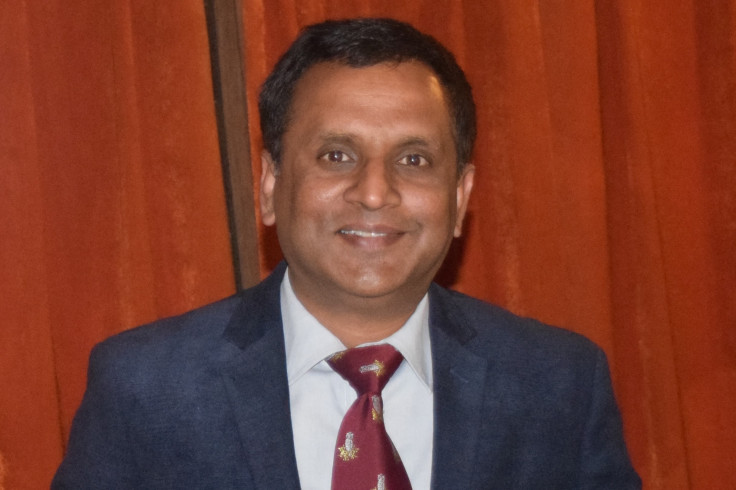
To understand what supply chain risks may occur in 2023, we reached out to Colonel Vikas Gupta (Retired), an Indian Army veteran with over 23 years of expertise in Supply Chain Management and logistics. He is also the Senior Vendor Manager at Amazon and is responsible for forecasting, pricing, and product launches. In a telephonic interview, he explains the four major risks that supply chain managers may have to steer through to minimize the impact of supply chain disruptions and challenges in 2023.
Shortage in Human Resources
The ongoing labor shortage is a challenge that will continue to persist. Despite being one of the most important jobs on the planet, trucking has struggled to attract enough workers to meet demands. Warehouse operations and manufacturing plants face similar challenges. Much of the current labor shortage is the result of external challenges such as pandemics, inflation, political instability, and so on.
Labor shortages in every industry have a knock-on effect on other industries, making this problem even more difficult to solve. Gupta, who has successfully led teams and operations in the retail sector amid the COVID-19 pandemic, stated that digitization and automation may be the key to solving these issues in the short term. He however emphasized that the shortage of labor can continue well into 2023 and 2024 so organizations need to establish themselves as more equitable employers who are willing to work towards retaining their employees instead of firing them.
"This change in organizational culture will take time to accomplish and will not happen overnight, but it's high time organizations start working along these lines," he said.
Cyber Threats
Cyberattacks on supply chains are becoming more common these days. According to an Accenture report published in May 2022, supply chain disruptions have resulted in a loss of €112 billion (0.9 percent of GDP) in the eurozone alone. Depending on the outcome of the Ukrainian conflict, these losses could reach €920 billion (7.7 percent of GDP) next year.
This issue has been building as supply chains have implemented more digital technologies. The massive digital transformation that is equipping the supply chain sector to deal with a disruptive norm is providing cybercriminals with ever-increasing opportunities to infiltrate businesses. "This is why supply chain cybersecurity platforms must keep up with evolving cyber threats and ensure that all attack vectors are always covered. A cyber-aware workforce, which includes all employees, is the best resource for developing this type of resilience," says Col.Gupta, who in his 20 years of military experience has handled the logistic troops and maintenance of defense equipment that were spread across 2000 kilometers and at an altitude of 17,000 ft above sea level in the Himalayas.
Bottlenecks
The maritime and logistics industries have been in a never-ending cycle of problems that have exacerbated congestion. Land capacity issues causing port and terminal congestion, a lack of railcars, and a lack of truckers and chassis have all had an impact on all trade participants. Bottlenecks in ocean freight are expected to remain a risk in 2023. A freight bottleneck is recurring traffic congestion on ocean highways caused by volume congestion, affecting port capacity. Consequently, this clogging of ports has had a domino effect on the entire supply chain. It has pushed warehouses to capacity and caused delays in delivery that has led to a lot of unhappy and unsatisfied customers.
According to Gupta, the only way supply chain managers can navigate through this problem is by implementing technologically driven processes using real-time data and predictive analysis. Supply chain managers need to use digital platforms which can handle demand planning and demand forecasting through real-time data monitoring of inbound and outbound assets.
Gupta who is responsible for inventory management for the North American and Canadian markets, stated, "digital transformation within the supply chain is a priority and companies should start investing in it. Being able to see real-time data, can make a huge difference in mapping out a plan to prevent disruptions in the supply."
Inflation
The supply chain is an interconnected operation, so when prices go up in one area, there is a ripple effect down the line. The current inflationary pressure is caused by increases in production costs such as wages, raw materials, energy, and transportation. According to the Economics Observatory, the Consumer Price Index in the United States increased by 5.4% in December 2021 over the previous year.
One way to accomplish this is to multi-source the supplier base with strict contract periods to account for sudden price changes explains the ex-military veteran, who today handles inventory and logistics of approximately $600M. "Keeping an eye on trends is also important here, as is managing the finances of your supply chain so that you're protected when the next wave of risks hits".
Conclusion
Managing supply chains will be a challenge regardless of the year. These four challenges will most likely drive supply chain change in 2023. Understanding and preparing for them ahead of time can help develop more effective crisis responses and prevent large-scale disruptions in the future.