Tesla Model 3 Quality Sacrificed To Hit Production Goals, Used Electric Tape For Cracks
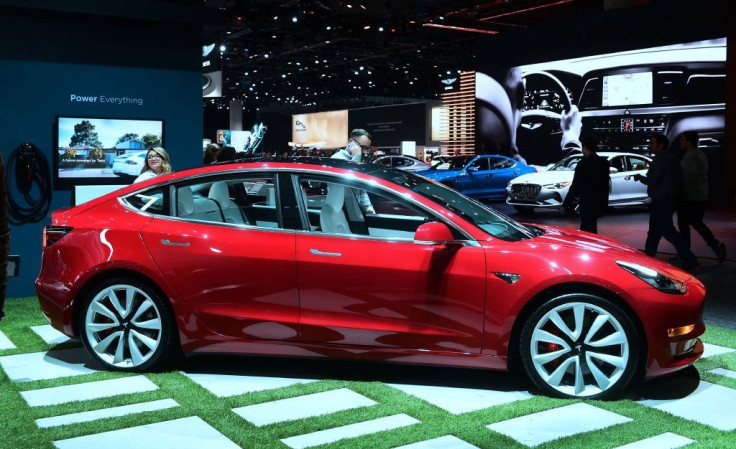
Now, we know exactly what Tesla CEO Elon Musk really meant by “production hell.”
Harassed workers at one production site at the Tesla Factory in Fremont, California claim management ordered them to take shortcuts to attain overly ambitious Model 3 production goals. These quick fixes, some of them clearly unsafe, included attaching broken plastic brackets with electrical tape instead of replacing them with new ones, and omitting some required vehicle tests.
The infractions took place at the open-air “tent” factory called “GA4” (General Assembly 4) established a year ago as a temporary site to expedite the production of Model 3s. GA4 has remained open, however, and has been kept open because of its importance to meeting Tesla’s enormous production targets.
According to employees interviewed by media, the “tent” produces 30,000 Model 3s per quarter. This massive total means workers assigned here have to assemble 120 Model 3s per shift and 2,160 Model 3s in a perfect six-day week.
Tesla has admitted the tent accounted for 20 percent of total Model 3 production during a high-output week in July 2018. Instead of becoming a temporary production site, the tent is now vital to Tesla’s production goals. Meeting lofty production targets, however, has come at the price of compromising quality and the physical exhaustion of workers.
Unlike the larger and automated factory nearby called “the brick,” production at the tent is almost entirely manual. Employees manually assemble Model 3 using brawn, power tools, lifts and conveyors. The tent has none of the sophisticated robotics inside the brick.
When plastic brackets and housings that hold critical electronics in place inside of the Model 3 break, supervisors told workers to use vinyl electrical tape to make quick fixes, according to a number of employees interviewed. Waiting for replenishment teams to deliver boxes of new plastic parts to their stations took too long and would delay production.
GA4 workers used vinyl tape to fix housings or brackets with cracks. They also applied tape to stop parts from vibrating if these parts weren’t fastened perfectly. Five employees said they were encouraged to take shortcuts to meet the tent’s production goals.
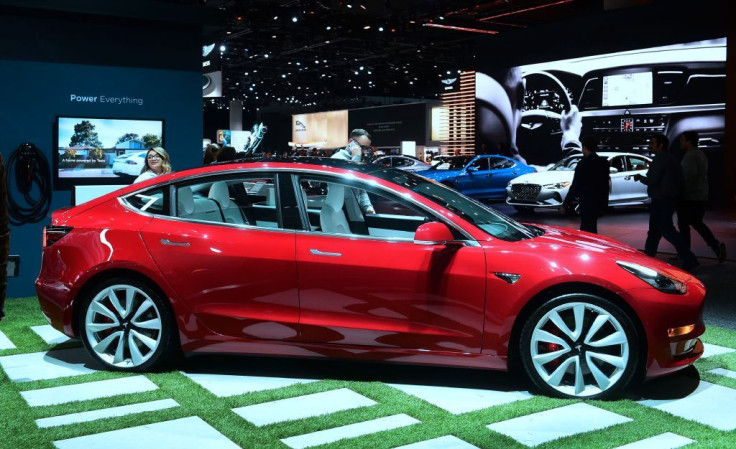
For its part, Tesla said it hasn’t found evidence of electrical tape being used to make quick fixes in GA4. It would never officially condone or encourage the use of tape for quick fixes.
The reliance on manual labor inevitably results in more defects. Workers suffer, too.
A former supervisor told CNBC he resigned after months of medical leave stemming from injuries he claims he sustained on the job. His wife, who also worked at the tent, said she was fired or using her mobile phone during a shift to book health appointments after an injury.
© Copyright IBTimes 2024. All rights reserved.