Yankee Barn Homes Turn Dreams Into Extraordinary Homes Through Custom Craftsmanship
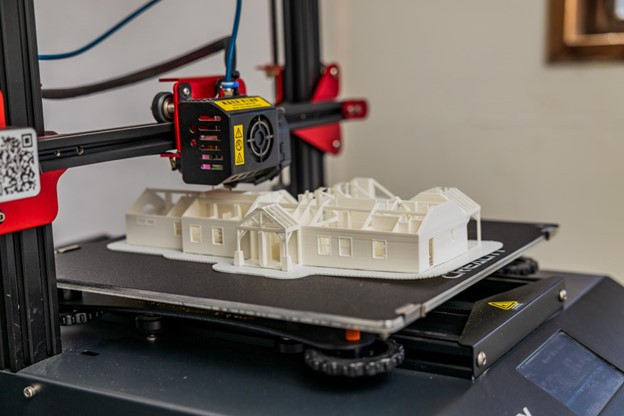
Building your new home is exciting, especially when you get a clear picture of how the process works. Yankee Barn Homes (YBH) truly understands this. For over five decades, the New Hampshire-based company has been a beacon of excellence in the niche market of boutique-styled prefabricated homes, specializing in custom post and beam construction. Behind their success lies a methodically orchestrated process, honed over years of experience, ensuring that each client's dream home is brought to life with unparalleled quality and efficiency.
The company uses a unique panelized shell construction process, allowing for quick post and beam-building work. The Douglas-fir timbers are kiln-dried, pre-cut, and pre-stained, resulting in a faster build. The True Wall and True Roof™ Panel System, constructed at the production facility, saves clients time and money on the job site by allowing parts to be shipped directly to the site with minimal assembly required. This overall prefabrication process allows for quicker custom home construction while ensuring high-quality components are in place. YBH builds any style of home, specializing in energy efficiency, ensuring a beautiful and lasting structure for future generations to cherish.
The design process for the home plans typically takes two to three months. Clients work with a project planner and designer to create their desired floor plan and exterior look. They can bring forth their own sketches and architectural drawings, or choose to work with an existing YBH floor plan.
From there, the magic unfolds as the client works directly with YBH's in-house project management team via the Buildertrend Client Portal. Kerri Post, COO of Yankee Barn Homes, elucidates on this initial phase, stating, "Our goal is to understand the client's vision intimately, whether it's drawn on paper or resides solely in their imagination."
As the process progresses, basic floor plans are drafted offering a glimpse into the spatial configuration and utilization of timber frame elements. The homes can be full timber frame, partial, or hybrid, depending on the homeowner's needs and aesthetics. The post and beam structure provides a flexible floor plan and open space volumes. This serves as a foundational blueprint upon which the design flourishes. Schematic plans follow suit, providing a more comprehensive overview accompanied by immersive 3D visualizations.
With the design crystallized, attention shifts toward component selections and final pricing. Every detail, from the style of the frame to the insulation values, is minutely curated to align with the client's preferences and budgetary considerations. Working with their local general contractor clients are able to finalize their total build cost estimates. Once finalized, the design undergoes rigorous scrutiny, ensuring compliance with local building codes and engineering standards.
The end of this phase marks the start of the next phase, that is, production, where YBH's seasoned craftsmen spring into action. As the components are prepared for delivery, anticipation reaches a crescendo for every homeowner. YBH's construction supervisor, alongside an optional skilled labor crew, oversees the assembly process on-site, ensuring seamless integration of every element.
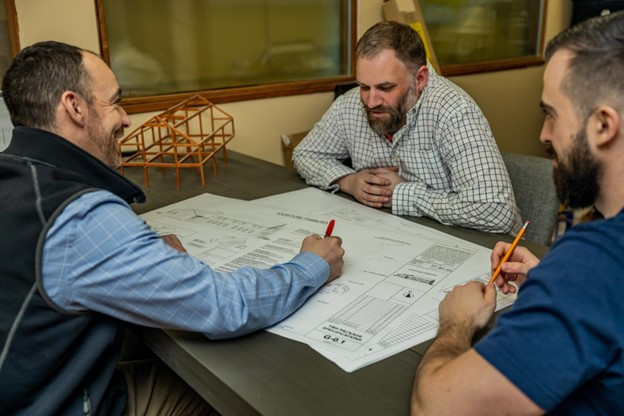
Once the custom home shell is assembled the focus then shifts toward finishing touches, handled by the client's builder. The home is meticulously built, encompassing foundation work, interior partitions, exterior siding, trim, roofing material, and utilities, ensuring a home that transcends mere bricks and mortar.
From conception to completion, the process embodies a symphony of collaboration, innovation, and unwavering dedication to excellence. Kerri reflects, "Our ethos is rooted in the belief that every home should be a reflection of its owner's unique vision and lifestyle. It's a privilege to play a role in turning those dreams into reality."
© Copyright IBTimes 2024. All rights reserved.