Back to His Roots: an American and the Business of Sugar Farming in the Philippines
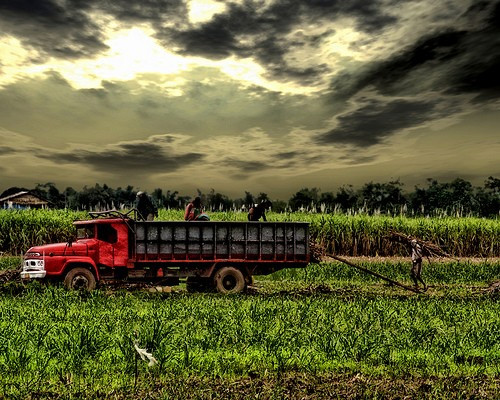
A sugarcane farm in the Philippines has been in James Ford's family for generations. It was the family business on his mother's side, and with the farm recently changing hands from one aunt to another, there was an opening for Ford to come and manage it.
Ford, a Filipino-American who grew up in Carlisle, Massachusetts, was born in the United States but lived in The Philippines as a child.
It was a unique opportunity to live in the Philippines and to re-learn a culture that I use to know, Ford said. I moved to U.S. in kindergarten and mostly lost touch with the culture.
In June, 2010, Ford left for Silay, an area on Negros Island, which is part of the Philippines' Western Visayas island chain, and about an hour south of Manila by plane. He was going to be living in a house surrounded by 20 square hectares (about 50 square acres) of sugarcane, some of it 12-feet high.
After acclimating to the new surroundings, the first thing that Ford did was take a five-day course on everything you need to know about growing sugar, he said. Sponsored by the Philippine's Sugar Regulatory Administration, the class covered things like soil pH levels, La Niña, tariffs and different growing techniques. There was even a teaching farm on site.
In the Philippines, sugar is at least a $1 billion per year industry. The country produces about 57 million pounds of sugarcane per year, making it the world's 10th biggest producer and the second highest in the region after Thailand.
Agriculture makes up 12 percent of the country's Gross Domestic Product (GDP), according to the CIA factsheet on the Philippines.
Ford said that sugarcane is a relatively relaxing crop. The most important thing is making sure that there is always cane growing and that the farm is constantly producing sugar.
Sugar takes 8-14 months to mature, but need fields to be constantly producing sugar. You have to make a timeline and calendar for each of the 10 fields, Ford said.
After it's harvested, the sugar is sold to a processing plant. The cane is sent there by train, and railway tracks actually run right through the farm to the plant.
There are sorts of metrics for measuring the quality, and eventually the sale price, of sugarcane. Weight is certainly a factor when selling it, but so is purity and sweetness.
Sweetness is measured from the juice inside the cane, Ford noted. The cane should be cut right before it reaches the best sweetness, so that it can be fully mature by the time it's finally processed, he added.
Working Internationally
There are unforeseen challenges when working abroad, things like the metric system, which you forget about until you arrive in a new country. There are also the vast cultural differences that really can't be grasped until arrival, such as the importance of family, which sometimes tends to squelch independence.
Another is the unforeseen difference between working in East Asia and the United States is the emphasis on manpower over machine-power.
It's all manual labor, Ford said. There are very few machines involved in the process. Everything is done by hand: harvesting, loading, even laying fertilizer.
There are a number of reasons for this, aside from the simple reason of tradition. In a country where labor is cheap, is the huge up-front cost of buying a tractor worth the long-term yields? There is also the issue of maintenance -- with the nearest repair shops often located miles away, as well as the problem of training laborers to work heavy machinery.
About 33 percent of the Philippines labor force is in agriculture, meaning about 13 million people, the highest of any sector. And on average, it takes 400 man-hours to harvest one hectare of sugarcane. With 20 square hectares on Ford's family farm, harvesting is no small task.
Learning the language was hard for Ford as well. The official languages of the Philippines are Tagalog and English, but there are said to be about eight different regional dialects of Tagalog (although the actual number is unknown). Where Ford was living people spoke Hiligaynon, commonly known as Illongo, which he already knew thanks to his grandparents and other relatives.
But even Illongo has its own sub-dialects and the language his family spoke was not the same as the one the farmers spoke.
The farmers speak in an old style of Illongo. Some words are same, some are same with different accents, some are different altogether, he said.
But bigger than the language barrier was the cultural barrier. Ford was born in the Philippines, now lived in the Philippines, but to the farmers, many of whom had even remembered him from when he was a baby, he was an American.
Some of the farmers had been working for my family for 30 or 40 years, Ford said. Getting their respect was a big challenge. They respected me as an individual, but some still saw me as a baby, and they all saw me as someone from the United States, who had all these different values.
The farmers reacted differently to me. In their mind, it'll be an American running and managing things. There was definitely some resentment and tension at first.
But Ford saw that has a challenge and not an obstruction.
That's when I decided to really talk to these guys: what are they scared of, what do they not want to happen? he said.
Once he did that, the only challenge left was getting used to the community into which he'd been accepted.
© Copyright IBTimes 2024. All rights reserved.